What is Plasma Cutting?
Plasma cutting was accidentally discovered by an inventor who was
trying to develop a better welding process. Though the technology
is still young today, plasma cutting is quickly changing the world
as we know it.
Plasma cutting is by far the simplest and most economical way to
cut a variety of metal shapes accurately. Plasma cutters can cut
much finer, faster, and more automatically than oxy-acetylene torches.
Because of their effectiveness, plasma cutters - especially CNC plasma
cutters (see below) - threaten to obsolete a large number of conventional
metalworking tools.
How a Plasma Cutter works
Basic plasma cutters use electricity to superheat air into plasma,
which is then blown through the metal to be cut. Plasma cutters
are extremely simple and require only a compressed air supply and
an AC power outlet to operate.
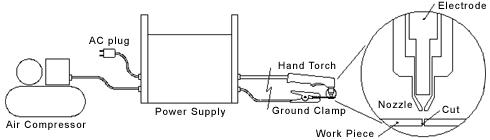
A complete plasma cutter consists of a power supply, a ground clamp,
and a hand torch. The main function of the power supply is to convert
the AC line voltage into a user-adjustable regulated (continuous)
DC current. The hand torch contains a trigger for controlling the
cutting, and a nozzle through which the compressed air blows. An
electrode is also mounted inside the hand torch, behind the nozzle.
Operation
- Initially, the electrode is in contact with (touches) the nozzle.
- When the trigger is squeezed, DC current flows through this
contact.
- Next, compressed air starts trying to force its way through
the joint and out the nozzle.
- Air moves the electrode back and establishes a fixed gap between
it and the tip. (The power supply automatically increases the
voltage in order to maintain a constant current through the joint - a
current that is now going through the air gap and turning the
air into plasma.)
- Finally, the regulated DC current is switched so that it no
longer flows through the nozzle but instead flows between the
electrode and the work piece. This current and airflow continues
until cutting is halted.
Notes
Plasma cutters are only useful for cutting metal. Non-conductive
materials like wood and plastic prevent the plasma cutter from doing
step 5 above.
The above steps describe the operation of a contact-type arc
starting plasma torch (the lastest technology). Old plasma torch
designs use high voltage sparks to bridge the gap between a fixed
electrode and tip when starting the arc. These old designs are not
recommended for several reasons (see link below).
The only parts of the plasma cutter needing frequent replacement
are the nozzle and the electrode. For this reason, these parts are
called "consumables."
click here if you want help selecting
a plasma torch
|